Специалистами ФТИМС НАН Украины в отделе формообразования под рук. проф. Шинского О.И. отработаны технологии получения отливок весом от 100 г до 5 и более тонн из различных металлов: чугуна, стали, алюминиевых, медных и специальных сплавов. Использовалось литье по газифицируемым моделям (ЛГМ) как наиболее недорогой и мало загрязняющий окружающую среду способ получения точных отливок.
Литейный цех, работающий по ЛГМ процессу, отличается от цехов литья в песчаные формы со связующим: 1) структурой; 2) технологическим процессом и оборудованием; 3) материальным и энергетическим обеспечением; 4) специализацией и количеством персонала. Отличия ЛГМ от других методов литья не касается процесса получения жидкого металла, плавильное отделение с шихтовым хозяйством не требует изменения. Определение необходимой массы жидкого металла производится по давно применяемой методике, с учетом того, что допуски на последующую механическую обработку элементов отливки (отверстий, пазов, наружных и внутренних размеров) составляют 0,2-0,5 мм и зависят в основном от способа получения пенополистироловой (ППС) модели.
Коренное отличие - в модельном и формовочном отделениях и отсутствии стержневого и смесеприготовительного отделения. Из-за того, что единственным формовочным материалом является природный кварцевый песок, выбивное отделение намного проще и имеет меньше технологического оборудования. Указанные отличия облегчают механизацию и автоматизацию всего литейного процесса, во ФТИМС НАНУ проведен комплекс работ и имеются разработанная технологическая и конструкторская документация практически по всем операциям ЛГМ с целью их полной или частичной автоматизации.
Формовочный песок постоянно находится в многократном обороте и его потери в среднем составляют 3-5% на одну заливку, отсутствие в нем связующего позволяет восстановить его для повторного использования без большого количества технологического оборудования и, соответственно, площадей. Выбивка отливки также не представляет трудности, т.к. сухой несвязанный формовочный песок легко высыпается из контейнерной формы, а очистка отливки не требует трудоемких операций как при литье в песчано-глинистые формы, не говоря уже о ХТС, ЖСС или по выплавляемым моделям. Формовочные, заливочные, выбивные площадки значительно чище, пыль, образующаяся при выбивке и др. операциях, легко удаляется местными вытяжными зондами с рабочих мест. Это способствует повышению культуры производства.
Термообрубное отделение ничем не отличатся, и для реконструируемых цехов можно использовать действующее, а для вновь создаваемого литейного цеха перечень и количество оборудования зависит от объема производства отливок и легко компонуется из стандартных единиц.
При литье стали следует учитывать, что в процессе замещения жидким металлом пенопластовой модели комплекс газов деструкции с общей формулой СnН2n+2, частично на глубину 0,05-0,15 мм от поверхности отливки повышает количество углерода, т.е. науглероживает ее. Поэтому для отливок из стали 20 и с более низким содержанием углерода подбором состава шихты учитывают возможное повышение количества углерода в стальной отливке до 0,1-0,2%, а также применяют ряд отработанных технологических методов, которые без труда позволяют лить заготовки из нержавеющей стали типовых марок.
Контроль качества отливок и их ремонт при переходе на ЛГМ намного упрощается. Как отмечалось выше, точность размеров и качество поверхности во много раз выше, чем при литье традиционными способами в формы, полученные в парных опоках. Повышение точности размеров и чистоты отливки экономит жидкий металл. Это достигается путем получения более точной (с учетом усадки металла) одноразовой модели в качественных металлических пресс-формах, соблюдения технологических операций при отсутствии снижающих точность отливки сборки формы и протяжки модели при формовке. Пенополистироловая модель дает точное воспроизведение отливки, позволяет проверить предъявляемые к детали требования по ее размерам и геометрии и без затрат средств до запуска детали в производство ввести необходимые конструкторские коррективы. Особенно такое преимущество ЛГМ проявляется при получении деталей с криволинейными поверхностями, свойственными лопаткам турбин, деталям насосов, коронкам зубьев и др. Еще одним преимуществом является возможность изготовления сложной и/или крупной пенопластовой модели поэлементно несложной сборкой в цельную модель.
Гибкость техпроцесса также характеризуется возможностью выбора из четырех широко применяемых способов получения пенополистироловых моделей: 1) вырезанием горячей струной из блочного полистирола; 2) фрезерованием на 3-х координатном станке с ЧПУ по чертежу детали; 3) выпеканием в автоклавах с камерой объемом от 100 до 1000 литров; 4) изготовлением на полуавтоматах методом теплового удара. Готовые модели собирают в модельные блоки с элементами литниково-питающей системы (ЛПС), сборку осуществляют тепловым способом или склеиванием. При малых размерах модели собирают в куст на одном стояке. Сборный блок/куст окрашивают и сушат. Высушенными их можно хранить очень долго, они не теряют своих размеров и свойств.
Специалисты ФТИМС разработали весь комплекс оборудования для получения моделей таким способом, что можно наблюдать на действующем участке литейного цеха института.
При отсутствии справочных материалов и методик проектирования отделений цехов ЛГМ процесса в технической литературе оптимальное планирование таких цехов пока не стало предметом рассмотрения в качестве конкуренции примеров удачного внедрения этой технологии в сравнении с другими литейными процессами. Проектирование цеховой планировки и всего технологического цикла как единого целого осуществляется для каждого случая исходя из требований заказчика с учетом наработанного (часто уникального) опыта внедрения разновидностей этого способа литья в различных странах. Используя универсальность и гибкость процесса ЛГМ, были спроектированы участки и цеха для единичного и серийного производства отливок, для ремонтных предприятий, количество и номенклатура оборудования которых резко отличаются как для изготовления моделей, так и для формовочно-заливочных операций.
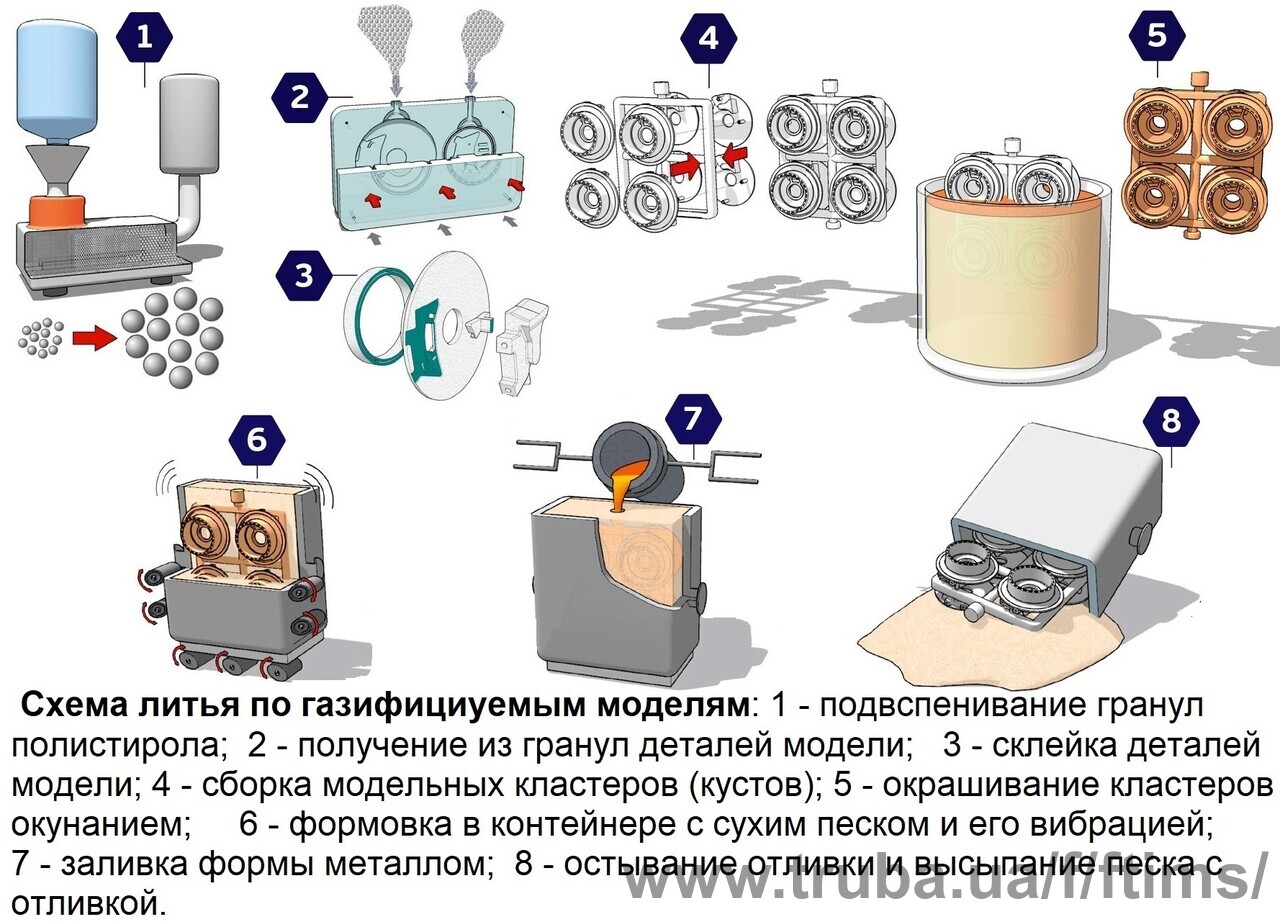
ФТИМС предложили проект реконструкции литейного цеха для производства отливок по газифицируемым моделям
Мнение редакции может отличаться от мнения автора.
+380 66 145 XX XX +380 66 145 7832
Идентификатор: 9590
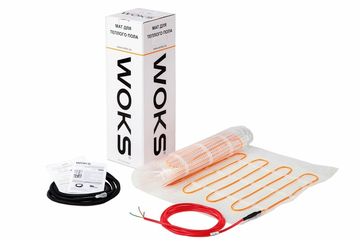
7 апр. 2025 г.
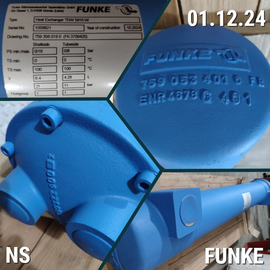
4 дек. 2024 г.